Green Building Community
The Next Generation of Housing – Prefabricated Homes
Posted by: Eileen Flynn // Student
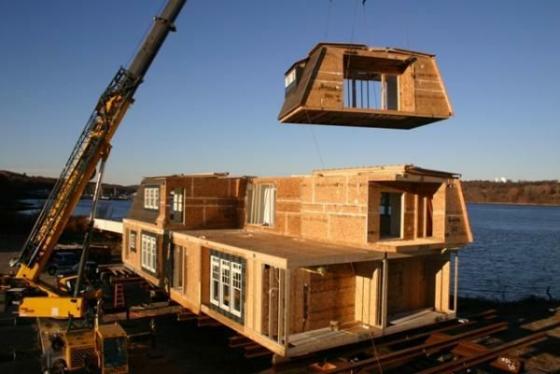
Traditionally, the process of constructing a house takes place on the same piece of land where the house will stay when completed. Construction teams travel to the same outdoor site for months and are forced to deal with space restrictions, weather conditions and other outdoor distractions. Most people are familiar with this way of home building and therefore tend to choose this option when starting their home from scratch. However, prefabricated houses are definitely worth considering. Prefabrication began in the United States in the early 1900s when the Aladdin Company began selling “house kits”. These kits were made up of all different house parts for owners to pick and choose from. The part would be constructed separately and then shipped to the site. The low costs of the “house kits” in the early 1900 is still the reason prefabricated homes could be a smart option today. A prefabricated home is technically any home that has a section built in a factory, which is later assembled to the house at the construction site. Modular and Panel buildings are both different categories of prefabricated homes. A Panel building is built by layering down each floor and then lowering each section of wall into place by a crane. A modular building is constructed by adding each box-like room one by one, also by a crane, and then securing all the pieces together. Both options for prefabricated homes save time and call for less construction workers, making each process more affordable for a home-owner. Many people worry that a prefabricated home would not be able to withstand intense winds or weather storms that a traditional constructed home could. David Cooper, president of Modular Homes Inc., says that modular homes are “built with more materials, they are constructed in factories that have it down to a science and are built sturdy enough to sustain the hurricane-force winds of being driven down the highway.” Fast-forward to the 21st century, just a few states west of where the revolutionary “house kits” were invented, California searches for a way to fight back against their affordable-housing crisis. Rick Holliday, a real estate developer near San Francisco, turns to history for help. Mr. Holliday recently opened Factory OS, a place where modular and panel homes can be manufactured away from the original construction site. These prefabricated homes are cheaper, less labor-intensive and environmentally friendly, exactly what California and so many other states need. Because of the many benefits, prefabricated homes are considered “the next generation of housing”. There has been a 15% annual expansion in prefab housing demand through 2017 in the United States, while other countries are way ahead of us in the movement. 123,500 shipments from US producers of prefabricated homes, valued at $7.3 billion, are expected through 2020. States that are struggling with affordable housing, like California and New York, are already starting to turn to prefabricated homes and will hopefully lead the rest of the country in that direction. Here are links with more information: https://www.nytimes.com/2018/06/07/business/economy/modular-housing.html https://home.howstuffworks.com/prefab-house1.htm https://www.ibisworld.com/industry-trends/market-research-reports/manufacturing/wood-product/prefabricated-home-manufacturing.html https://revolutionprecrafted.com/blog/the-rise-of-the-prefab-market-around-the-world-infographic/ https://www.freedoniagroup.com/Prefabricated-Housing-Market-In-The-US.html
PatPrince317 // Lifelong Learner and Green Energy Aficionado
You used to be able to buy those houses in the Sears catalog. You see a bunch of them in Massachusetts, although they have usually had additions added on over the past 100 years.
Ideally, they are the way to go. First is that they deal with the labor shortage in the construction industry - you only need a few people to assemble the house once it's delivered.
Second, they are made in factories that go through a lot more quality inspection than a traditional building inspector.
In terms of insurance, they like these homes better because they are more sturdy and are consistent when it comes to replacement cost and underwriting. That's not to say they're cookie cutter. These are very populat in London as rooftop affitions as real estate is very expensive there.
Please be kind and respectful!
Please make sure to be respectful of the organizations and companies, and other Rate It Green members that make up our community. We welcome praise and advice and even criticism but all posted content and ratings should be constructive in nature. For guidance on what constitutes suitable content on the Rate It Green site, please refer to the User Agreement and Site Rules.
The opinions, comments, ratings and all content posted by member on the Rate It Green website are the comments and opinions of the individual members who posts them only and do not necessarily reflect the views or policies or policies of Rate It Green. Rate It Green Team Members will monitor posted content for unsuitable content, but we also ask for the participation of community members in helping to keep the site a comfortable and open public forum of ideas. Please email all questions and concerns to admin@rateitgreen.com